Have you ever wondered why some PEB projects end up five times higher than the originally quoted amount? It’s no secret that PEBs are inherently cost-effective and have faster construction time than any conventional type of building. Still, from time to time, costs seem to run absolutely out of control.
PEBs are indeed a smart choice for any industrial, warehouse, or even commercial building as they save time and money. Well, there is a catch; minor errors in the design, planning, or construction processes can soon get out of hand and turn what seemed to be a low-cost project into something that breaks the bank.
We give you the 10 most common PEB mistakes that increase costs to help you sidestep this trap.
Common PEB Mistakes That Increase Costs

1: Mistake #1: Poor Site Preparation
Poor site preparation is one of the most common and costly mistakes in PEB projects. Due to poor preparation, delays are caused and even higher costs ensue. Sites not well tested may develop foundation problems that may further make the whole construction much more complicated.
How to Avoid It: Perform thorough soil tests and site clearance before construction. Proper planning upfront will help save time and money otherwise wasted in correcting it later on.
2: Mistake #2: Choosing the Wrong PEB Design for the Function
This is because it shows a wide range of design possibilities and being wrong can be disastrous. There is, for example, the issue of under-sizing or over-sizing the structure for specific functional needs in your case. Resources will thus be wasted, and usability will be minimized or costly adjustments will be required at later stages.
How to Avoid It: Spend time on proper planning. Collaborate with professionals who understand your business and the needs of your building so that the design addresses the current as well as future requirements.
3: Mistake #3: Underestimating Future Requirements
A lack of planning for future growth or space changes can become something of a budgetary nightmare. Planning without flexibility may require costly structural changes down the road if your needs change over time.
How To Avoid It: Design for future growth and change by using modular designs that allow easy expansions with less disruption and cost.
4: Mistake #4: Inaccurate Material Estimates
Underestimation regarding steel, for example, can prove costly. It lands you with surprise orders and rush fees if you underestimate them. The opposite case is waste in case of overestimation when you don’t need the same.
The Way to Avoid It: Always work with precise design parameters. Use experienced vendors that will give you reliable estimates based on a comprehensive review of your project.
5: Mistake #5: Skipping Structural Load Considerations
If you do not account for loads such as wind, seismic activity, or snow loads, you could find yourself facing dangerous conditions and higher costs when you start scrambling at the last minute to correct mistakes.
Prevention: Conduct environmental assessments early in the design stage so you understand what load-bearing capacity your PEB will have to endure. These assessments should be the guide for material and design selections.
Design and Construction Errors That Lead to Higher Costs
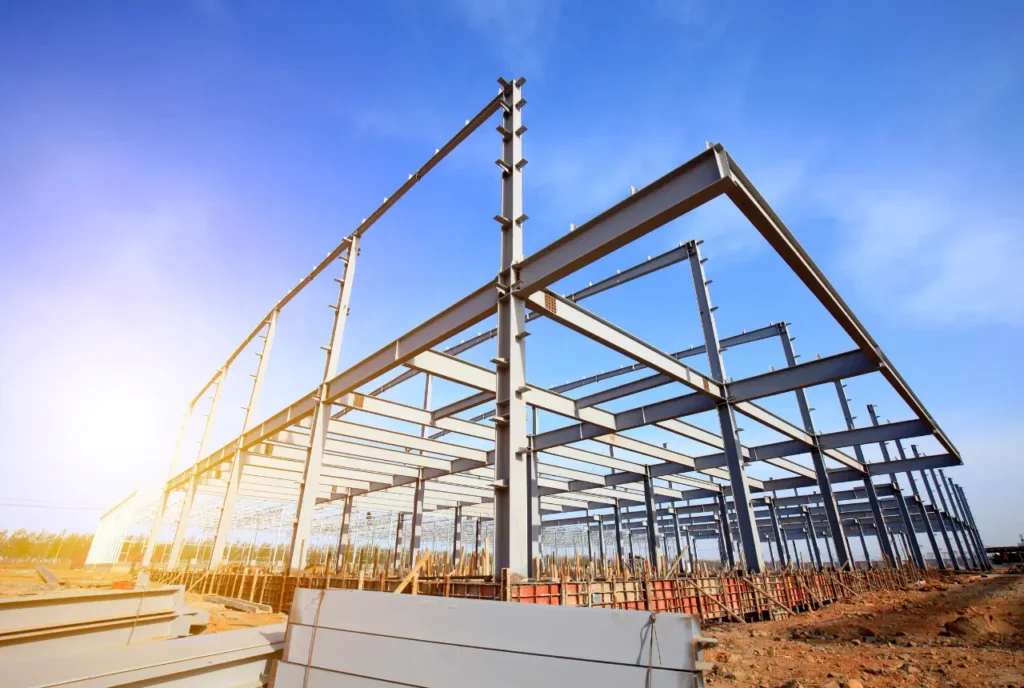
6: Mistake #6: Ignoring Local Building Codes and Regulations
That way, you might spend your whole budget on burning due to non-compliance. Fines might be quite expensive, and delays may cause problems, and sometimes even complete redesigning is required.
How to Avoid It: Work closely with local authorities to ensure your design will comply with all the regulations. Better still, consult a local expert who knows the ins and outs of the process.
7: Mistake #7: Lack of Proper Drainage and Insulation Planning
Poor planning on places such as drainage and insulation can easily lead to costly long-term problems in the form of water damage or insufficient energy efficiency. In such a scenario, you save money upfront by skipping these elements but pay dearly for it in the long run.
How to Avoid It: Always ensure drainage systems and sufficient insulation in the designing phase. This saves one from structural damage and lesser levels of maintenance going forward.
8: Mistake #8: Miscommunication with the Contractor
Miscommunication between you and your contractor is the most common source of error in the final product. Small details, when misunderstood or overlooked, can become expensive fixes.
How to avoid it: You have to establish clear communication channels from the very beginning. Regular meetings should be done with detailed documentation and constant updates to ensure that everyone is on the same page.
Budget and Vendor Management Mistakes That Increase Costs

9: Mistake #9: Choosing the Wrong Vendor
The vendor you choose can make or break your project. Less experienced or less reliable vendors may quote at a lower price, but they tend to cost more in the long run because of delays, substandard materials, and hidden costs.
How to Avoid It: Don’t select a vendor based on price alone. Be sure to vet your potential vendors by reviewing their previous projects, checking references, and assuring that they have experience working on PEB construction.
10: Mistake #10: Skipping Maintenance and Long-Term Considerations
Once your PEB is built, failure to conduct regular maintenance will result in increased repair costs, loss of structures, and a shorter building lifespan. Some of the minor issues might quickly evolve into enormous problems as far as the cost factor is concerned if you allow routine inspections to fall through.
How to Avoid It: Budget for and commit to regular inspections and maintenance. Then build a long-term care plan so you can catch problems before it become a major repair issue.
Conclusion
There are many benefits of pre-engineered buildings, but some potential pitfalls may propel your costs high. From site preparation, and vendor selection, to post-construction maintenance, every phase in the process deserves adequate thought to avoid making costly mistakes.
The key to success in a PEB project is proper planning, finding the right professionals, and being involved in all steps of the process. You should address the potential for mistakes before they can happen to make sure your investment into a PEB will remain on track and within budget – to provide the structure you need today and tomorrow.
So remember: avoid the mistakes, keep it long-term, and work with good teams. Voila! Your PEB project then should be smooth sailing.