There are many PEB structure design factors that influence construction. PEB structures have gained significant popularity in the construction industry due to their cost-effectiveness, efficiency, and rapid construction. This trend underscores the importance of meticulous design to ensure the success of PEB projects.
In this post, we delve into five crucial design factors that play a pivotal role in the overall performance and longevity of PEB structures. From structural integrity and load considerations to architectural flexibility and sustainability, a comprehensive understanding of these factors is essential for architects, engineers, and project stakeholders engaged in PEB construction.
II. Understanding PEB Structures
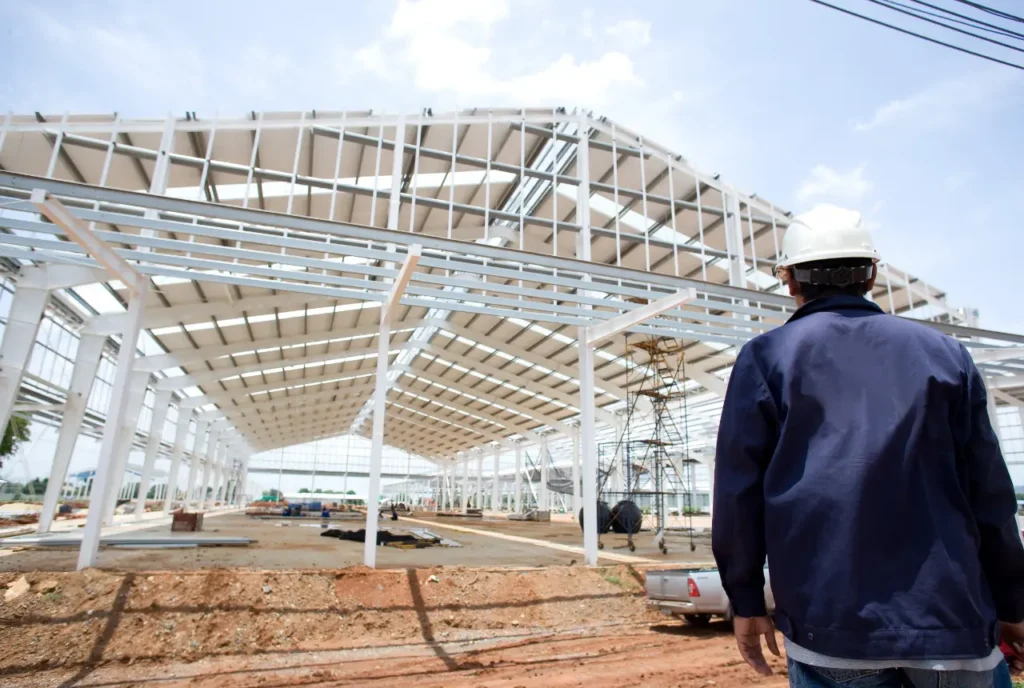
To understand Pre-Engineered Building design, we will have to understand what it stands for. When referring to Pre-Engineered Building (PEB) it means the structural system where components are pre-designed. These structures are manufactured off-site and then carried to the construction site for assembly.
The key components of PEB include structural elements such as rigid frames, columns, beams, and roofing and wall panels. These components are typically made of steel, offering durability and strength.
What is the advantage of having PEB structure design standards?
The advantages of PEB structures are manifold –
- First, they significantly reduce construction time as components are prefabricated, leading to faster project completion.
- The time efficiency also contributes to cost-effectiveness, making PEB an economically viable option.
- Additionally, the use of standardized components in PEB systems minimizes waste, promoting sustainability in construction practices.
The other type of advantage that PEB structures provide is the diversity of application. The design flexibility allows customization. This could cater to different needs for different spaces like warehouses and factories and many more.
PEB is also prevalent in commercial buildings, sports arenas, and aircraft hangars. The inherent efficiency and versatility of PEB structures make them a compelling choice for various construction projects
III. 5 Must-Know PEB Structure Design Factors
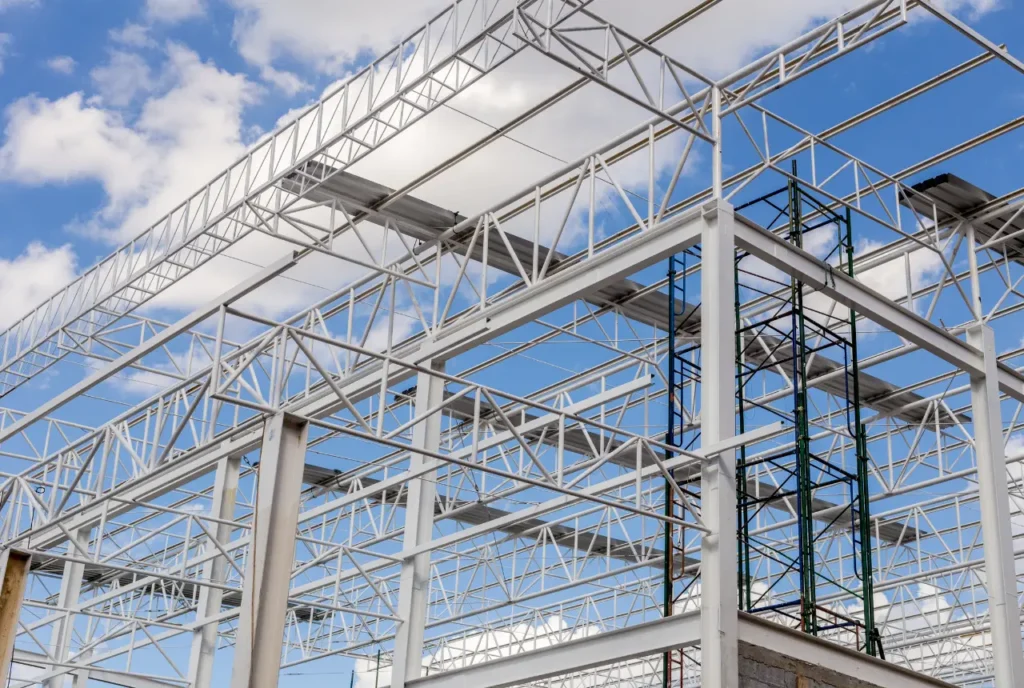
Design Loads: The Backbone of Strong PEB Structures
In the new age, Pre-Engineered Buildings have become the wonders of modern engineering. Hence, their strength and safety lie in the crucial element of design loads. The loads are created to paramount the acting forces and loads on the structure. Constructed after accurate calculations, design loads are necessary for structural integrity.
What are the different types of Loads?
- Dead Loads – This includes the frames, cladding, and permanent fixtures. This takes the load of the constant weight of the PEB that acts vertically downwards.
- Live loads – These loads can be static or dynamic. Live loads or moving loads provide variable forces due to occupants, furniture, equipment, and stored materials.
- Wind loads – These refer to the horizontal forces exerted by wind pressure. Wind loads can vary based on location, structure shape, and wind speed. Structural integrity is an absolute necessity for the structure to withstand these types of loads.
- Snow Loads – Accumulated snow exerts vertical pressure on structures. These are only relevant in snowy regions, which depend on the slope of the roof and the density of snowfall.
- Seismic Loads – Earthquakes are known for giving massive pressure to structures. With horizontal and vertical forces. It becomes crucial to have flexible structuring in seismically active areas. These are determined by location and earthquake intensity.
Accurate Calculations: Why They Matter:
Accurate calculations are absolutely important for the proper structuring of building constructions. Underestimating the pressure of any load could lead to disastrous consequences. PEB structures that are constructed for storage and other purposes need detailed structuring. Overlooking elements of snow accumulation and wind pressure could lead to roof collapse and structural failure, respectively.
Precise load calculations ensure the PEB can withstand all expected forces, safeguarding lives and property.
Factors Influencing Calculations:
- Location – It is important to detect safe building construction. Wind and snow loads vary significantly by region, where structural integrity and material strength are crucial. Earthquakes could be considered seismic zones, as they dictate the earthquake intensity.
- Occupancy – The occupancy requirements differ with sites. As warehouses have different requirements than offices. It is important to calculate the intended use that determines live loads.
- Purpose – The purpose differentiator for a school building varies from factories. Industrialized areas create higher dynamic loads due to their heavy machinery.
Design Standards:
Standardized codes like IS 875 (India) and ASCE 7 (USA) provide guidelines for calculating different types of loads based on location, occupancy, and structure type. These codes are crucial for ensuring safe and responsible PEB design.
B. Material Selection
A structural system known as a “pre-engineered building” (PEB) has its components pre-designed and built off-site, ready to be assembled at the construction site. Structural elements like stiff frames, columns, beams, roofs, and wall panels are among the main constituents of PEB.
PEB structures provide numerous benefits. First off, because the components are prefabricated, they drastically cut down on construction time, resulting in a quicker project completion. PEB is a financially feasible choice because of its cost-effectiveness and time efficiency.
PEB structures are used in many different contexts; notable examples are factories and warehouses. Because of PEB’s design flexibility, solutions can be tailored to meet particular requirements. PEB is also widely used in business buildings, airplane hangars, and sports arenas.
C. Connection Details
While the strength of individual components is crucial, a PEB’s true stability lies in its connections. Just like a chain is only as strong as its weakest link, poorly designed connections can render even the sturdiest members useless.
Why Are Connections Critical?
These unsung heroes silently transfer loads between PEB elements, ensuring the entire structure acts as one cohesive unit. Imagine a roof held up by weak bolts – a single gust of wind could spell disaster. Proper connection design prevents such failures, guaranteeing the building’s integrity and safety.
Bolted vs. Welded Connections:
Two main types of connections dominate PEB construction: bolted and welded. Bolted connections offer quick assembly and easy inspection, while welded connections provide superior strength and ductility. The choice depends on factors like load transfer requirements, ease of construction, and cost.
The Art of Welding:
When welding comes into play, qualified welders and strict procedures are paramount. Improper welds can introduce defects, jeopardizing the connection’s strength and leading to premature failure. Utilizing certified welders who follow approved procedures ensures reliable and robust connections.
Optimizing with Software:
Modern advancements bring PEB structure design software into the mix. These tools analyze connections, considering complex factors like material properties, loads, and weld characteristics. They help optimize connection design, suggesting the most efficient and cost-effective solutions while ensuring structural integrity.
D. Design Software and Standards
The world of PEB design has transcended manual calculations and entered the digital realm. Today, powerful design software like STAAD.Pro and Tekla Structures are the architects of these robust structures.
Modelling, Analysis, and Optimization:
These software wonders go beyond mere drawing tools. They create detailed 3D models of the PEB, taking into account material properties, connections, and loading conditions. Powerful analysis engines then simulate real-world forces, allowing engineers to assess stress, deflection, and overall structural behavior.
Adhering to Standards: The Safe Haven of Codes:
But even the most sophisticated software needs guidance. This is where design standards like IS 800 (India) and IBC (USA) step in. These codes establish guidelines for various load calculations, member sizes, and connection details, ensuring structures comply with safety regulations and withstand anticipated forces.
Human Expertise: The Guiding Hand:
Software is a powerful tool, but it shouldn’t replace experienced engineers. Their knowledge of design principles, code interpretations, and practical experience enables them to effectively utilize software and navigate the complexities of standards.
E. Design Optimization
Building a strong PEB is only half the battle. In today’s world, design optimization is critical for achieving cost-effectiveness and material efficiency. It’s about squeezing the most out of every component, ensuring the structure fulfills its purpose without unnecessary bulk or expense.
Optimizing the Recipe:
PEB design optimization involves strategically adjusting various elements. Span lengths, for instance, can be optimized to reduce the number of supporting columns, saving material and construction costs. Member sizes can be carefully selected to meet load requirements without overdesigning, minimising material usage.
Technology & Expertise: Hand in Hand:
Achieving optimal design isn’t a simple puzzle. This is where powerful software steps in. Tools like those mentioned earlier can analyse numerous design iterations, suggesting material combinations, span lengths, and connection details that deliver the best balance of strength, cost, and efficiency.
Beyond the Initial Cost: Life Cycle Analysis:
The benefits of optimization extend beyond initial construction costs. Life cycle cost analysis takes a broader view, considering factors like maintenance, energy efficiency, and even end-of-life disposal. Optimized designs often lead to lower maintenance needs, reduced energy consumption due to lighter structures, and even opportunities for reusing materials at the end of the PEB’s lifespan.
Conclusion
We’ve explored the five crucial pillars of successful PEB design: understanding design loads, prioritizing robust connections, leveraging powerful software and standards, and optimizing cost and efficiency. Each factor plays a vital role in ensuring the safety, durability, and cost-effectiveness of your PEB project.
Remember, navigating these complexities requires specialized expertise. Qualified engineers possess the knowledge and experience to translate your vision into a safe, functional, and optimized PEB. They understand the interplay of these design factors and ensure your structure adheres to relevant standards.
Don’t hesitate to involve professionals early in the process. Their expertise will save you time, and money, and ensure your PEB stands strong for years to come. Invest in expert design, and build your vision with confidence.