Pre-Engineered Buildings (PEB) represent a modern construction approach wherein structural components are manufactured off-site and then assembled on-site. This method offers efficiency, cost-effectiveness, and flexibility in design, making it increasingly popular in the construction industry.
Amidst the rising concern about material waste in traditional construction, PEB stands out as a sustainable alternative. Traditional construction often generates excessive waste due to inaccurate measurements, overordering of materials, and on-site modifications.
This not only leads to environmental degradation but also contributes to higher costs. PEB minimizes material waste by precisely fabricating components in a controlled factory environment, ensuring optimal use and reducing the environmental impact of construction activities. In this blog, we address how PEB structures reduce material wastage.
The main argument for PEB lies in its potential to significantly decrease material waste, making it an environmentally friendly and economically viable solution for sustainable construction practices.
Benefits of PEB Structures for Material Efficiency
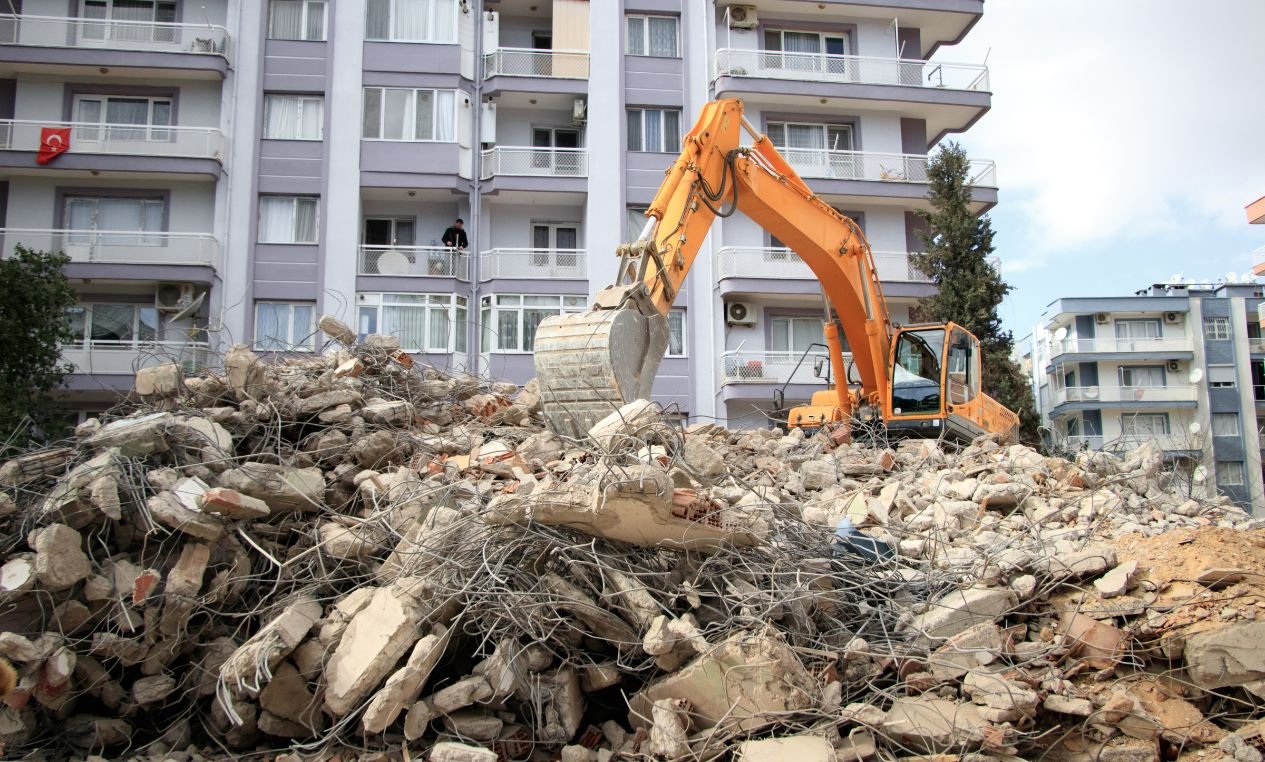
1. Precise Engineering and Manufacturing:
Computer-aided design (CAD) software plays a crucial role in optimizing material usage in construction, particularly in Pre-Engineered Buildings (PEB). CAD enables precise and detailed planning of structural components, allowing for accurate measurements and minimizing design errors. This accuracy translates into efficient material utilization, as CAD allows for optimal nesting of components on raw materials, reducing waste.
In the controlled factory environment of PEB manufacturing, CAD designs are translated into precise cutting instructions. This precision minimizes cutting errors, ensuring that materials are used efficiently and minimizing scrap generation. Unlike on-site construction, where adjustments often lead to excess material waste, the use of CAD in PEB promotes a streamlined and precise manufacturing process. The result is not only cost savings but also a significant reduction in overall material waste, contributing to sustainable and environmentally conscious construction practices.
2. Standardized Components and Modular Design:
Prefabricated components in construction, like those in Pre-Engineered Buildings (PEB), minimize cutting and onsite adjustments, thereby reducing waste. These components are manufactured with precision in a controlled factory environment, aligning with exact specifications from computer-aided design (CAD).
This eliminates the need for on-site alterations and reduces material wastage associated with cutting errors. Additionally, the flexibility of modular design allows for customization to specific project requirements. As a result, excess materials are minimized since components are tailored to fit seamlessly, optimizing material usage and contributing to a more sustainable construction process.
3. High Strength-to-Weight Ratio of Steel:
PEB structures utilize less steel compared to traditional methods due to the inherent strength of the pre-engineered components. The efficiency in design ensures that the structural elements bear loads effectively, allowing for a reduction in the overall steel quantity required. This not only minimizes raw material usage but also has a cascading effect on reducing transportation needs.
With lighter components, the transportation of materials to the construction site becomes more resource-efficient, leading to lower energy consumption and greenhouse gas emissions. The decreased reliance on steel and optimized transportation contribute to a reduction in the embodied energy of the materials, making PEB a sustainable choice in construction.
PEB Structure Components and Material Wastage
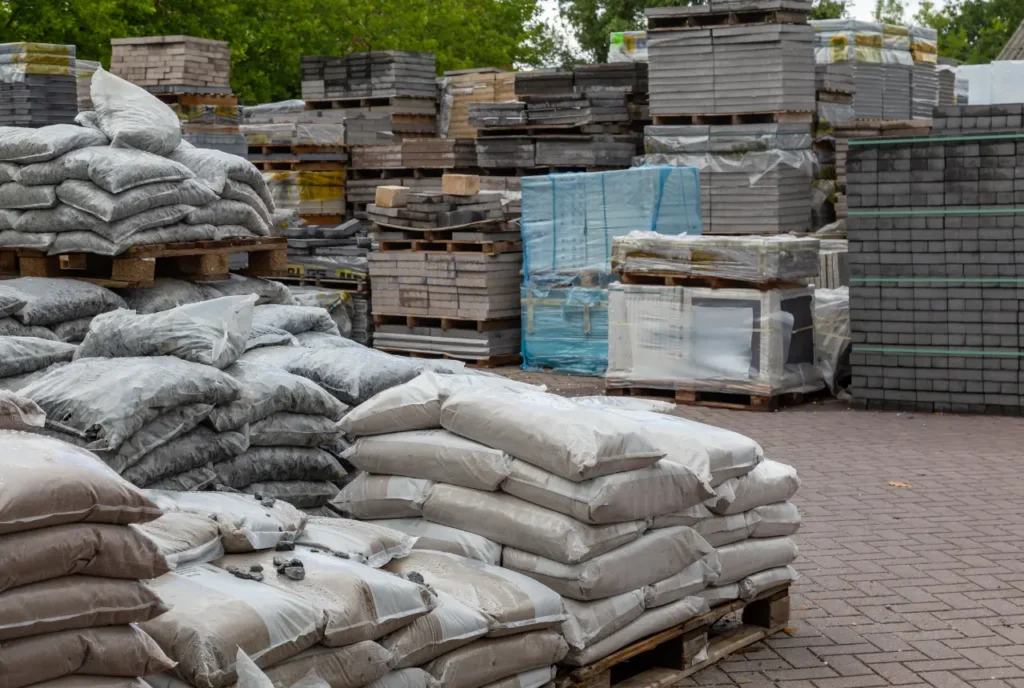
1. Primary Components:
Pre-Engineered Buildings (PEB) consist of key components such as primary columns, secondary beams, and purlins. Primary columns, typically I-shaped, bear the vertical loads, while secondary beams connect columns and support the roof. Purlins, horizontal elements, provide additional support for roofing materials. Each component is crucial for the structural integrity of the building.
Precise pre-fabrication in PEB minimizes waste generation for each component. Advanced manufacturing processes, guided by computer-aided design (CAD), ensure accurate measurements and efficient material use. In the controlled factory environment, columns, beams, and purlins are fabricated with minimal cutting errors, reducing scrap generation.
The modular nature of PEB allows for customization without on-site adjustments, further minimizing waste. This precision not only enhances the structural efficiency of the components but also contributes to the overall sustainability of PEB structures by optimizing material usage and reducing environmental impact.
2. Secondary Elements and Cladding:
In Pre-Engineered Buildings (PEB), pre-cut and sized sheets for wall and roof cladding contribute to the reduction of onsite wastage. These sheets, fabricated with precision in a controlled factory environment, align with exact measurements and specifications. This eliminates the need for on-site cutting and reduces material waste associated with inaccuracies or adjustments.
Moreover, the use of recycled or sustainable materials in cladding options further enhances the eco-friendliness of PEB structures. Many PEB manufacturers offer cladding materials made from recycled content or sustainable sources. This approach not only minimizes the environmental impact of construction but also aligns with the growing emphasis on sustainable practices in the building industry.
By incorporating recycled or sustainable materials in cladding, PEB structures can contribute to resource conservation and promote a more environmentally conscious approach to construction.
How to Design PEB Structures for Minimal Material Wastage
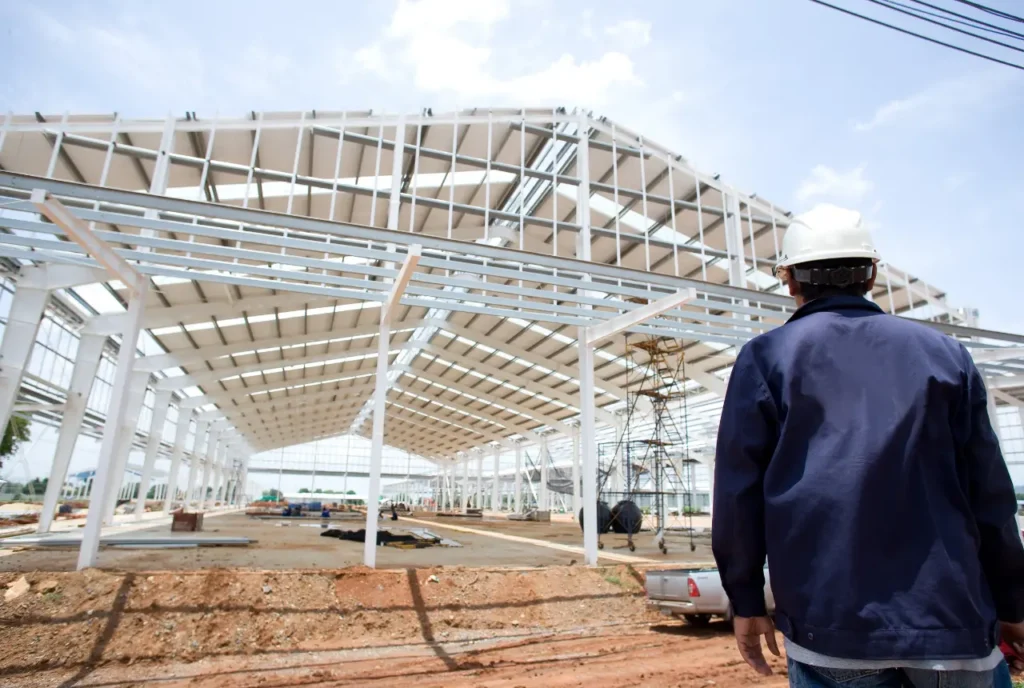
1. Optimizing Span and Spacing:
Carefully chosen spans and spacing between components in Pre-Engineered Buildings (PEB) play a crucial role in minimizing material usage. Structural engineers and designers meticulously determine optimal dimensions based on load requirements and structural efficiency. This strategic planning ensures that the materials used, such as columns, beams, and purlins, are deployed in a way that meets safety standards while minimizing excess.
Software plays a pivotal role in this process by simulating load distribution and optimizing material allocation. Computer-aided design (CAD) and structural analysis software allow for precise modeling and simulation of various load scenarios, enabling engineers to fine-tune the design for efficiency.
By leveraging these tools, PEB designers can make informed decisions about component sizes, spans, and spacing, ultimately reducing the overall material requirements. This approach not only enhances structural integrity but also aligns with sustainable construction practices by minimizing material waste.
2. Modularization and Customization:
Modular design enables the efficient use of standard components in construction with minimal modifications. In a modular approach, standardized elements like walls, floors, and structural components are designed to fit together seamlessly, reducing the need for customization.
This results in cost savings, quicker assembly, and enhanced efficiency in material utilization. Standardization allows for economies of scale in production and simplifies logistics during both manufacturing and construction phases.
Considering future expansion needs is crucial in modular design to avoid material redundancy. Anticipating potential changes in space requirements allows for the incorporation of flexible designs that can accommodate expansion without unnecessary dismantling or replacement of existing components.
This foresight not only promotes sustainability by minimizing material waste but also ensures that the initial construction aligns with long-term needs, making the building adaptable and resource-efficient over its lifecycle.
3. Waste Management and Recycling:
On-site waste management in construction involves sorting and segregating materials for responsible disposal. Strategies include establishing designated waste collection areas, training workers on proper disposal practices, and collaborating with recycling facilities.
Steel, a common material in construction, is highly recyclable. Scrap steel from Pre-Engineered Buildings (PEB) can be recycled into new steel products. Additionally, the modular nature of PEB allows for components to be easily disassembled and reused in future projects, minimizing overall waste.
Incorporating these practices not only reduces the environmental impact but also promotes sustainability by extending the life cycle of materials and minimizing the need for new resource extraction.
Material Wastage in PEB Construction and its Environmental Impact
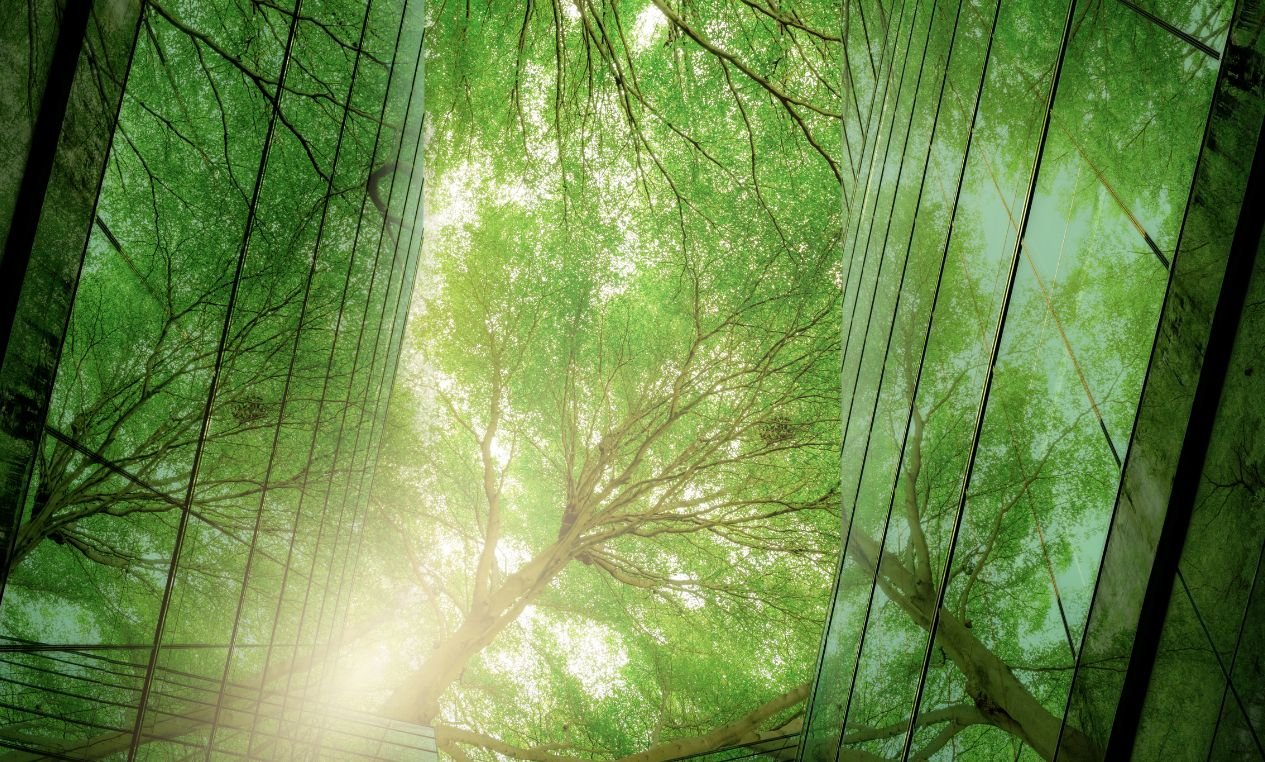
1. Quantifying Material Wastage Reduction:
Various studies, including research by the Metal Building Manufacturers Association (MBMA), consistently demonstrate a significant reduction in material waste with Pre-Engineered Buildings (PEB) compared to traditional construction methods. PEB construction showcases waste reductions ranging from 20% to 30%, as precise off-site fabrication minimizes errors and on-site adjustments.
This efficiency, coupled with controlled manufacturing guided by computer-aided design (CAD), leads to a notable decrease in overall waste generation and resource consumption. Such data underscores PEB’s role as an environmentally sustainable and resource-efficient alternative in the construction industry.
2. Environmental Benefits of Reduced Waste:
The connection between material waste and environmental impacts is significant, as waste in construction contributes to a higher carbon footprint and resource depletion. Traditional construction methods, characterized by inaccuracies, on-site adjustments, and overordering of materials, result in excessive waste, leading to increased energy consumption and emissions associated with material production and disposal. Additionally, the depletion of natural resources in the extraction and processing of raw materials exacerbates environmental strain.
How PEB structures reduce material wastage is by translating to lower energy consumption and emissions. The precise off-site fabrication and minimal on-site adjustments in PEB construction not only decrease the need for excess materials but also mitigate the environmental impact of resource extraction and manufacturing processes.
As a result, PEB represents a sustainable solution, minimizing both material waste and the associated environmental burdens of energy consumption and emissions.
3. Life Cycle Assessment of PEB Structures:
Life Cycle Assessment (LCA) is a comprehensive evaluation method that assesses the environmental impact of a product, process, or building throughout its entire life cycle. It considers resource extraction, manufacturing, transportation, use, and disposal phases, providing insights into the overall environmental footprint. LCA is crucial in sustainability as it helps identify opportunities for improvement and informs decision-making to minimize environmental impacts.
LCA studies consistently highlight the sustainability benefits of Pre-Engineered Buildings (PEB). Due to precision in design, controlled manufacturing, and reduced on-site waste, PEB structures exhibit lower environmental impacts compared to traditional construction. These studies emphasize the positive correlation between the efficient use of materials in PEB and a reduced overall environmental footprint, making them an environmentally responsible choice in the construction industry.
Conclusion
Pre-Engineered Buildings (PEB) structures reduce material waste through precise off-site fabrication, minimizing on-site adjustments. The controlled manufacturing environment and modular design optimize material usage, lowering overall environmental impact.
PEB’s efficiency aligns with responsible construction practices, promoting sustainability by decreasing resource consumption and lowering carbon footprints. Embracing PEB technology represents a pivotal step toward building a greener future, emphasizing the importance of innovative, eco-friendly construction methods in fostering environmental stewardship and creating more sustainable structures.