PEB structure maintenance is easier in comparison to other structures. Pre-engineered buildings (PEBs), also known as metal building systems, are a popular and versatile construction option. These buildings are designed and manufactured off-site using standardized components, then assembled on location.
This approach offers faster construction times and cost savings compared to traditional methods. However, to ensure their long-term performance and maximize their lifespan, proper maintenance of PEBs is crucial. Regular inspections and proactive measures can prevent costly repairs and disruptions, keeping your PEB functioning optimally for years to come.
Understanding PEB Structures
The core of a PEB lies in its steel frame, consisting of two main categories, understanding which could help in PEB Structure Maintenance.
- Primary frames: These are the heavy-duty components like columns (upright supports) and rafters (roof beams) that form the main structure. They are typically built with I-beams for strength.
- Secondary frames: These lighter components include purlins (supporting bars for the roof and walls) and girts (supporting strips for wall cladding). They are often made from C-sections or Z-sections.
The frame is then enclosed by cladding, typically made from metal sheets or sandwich panels. These panels can be single-skin (offering basic weather protection) or double-skin (incorporating insulation for temperature control).
PEB design involves creating a customized plan considering factors like building size, purpose, and local weather conditions. The components are then fabricated in a controlled factory setting, ensuring quality and precision. This allows for efficient assembly on-site, where the pre-made parts are bolted together.
Benefits of Proper PEB Maintenance
By prioritizing proper PEB Structure Maintenance, you reap numerous benefits:
- Extended lifespan: Regular inspections and timely repairs can prevent minor issues from escalating into major problems, significantly extending the life of your PEB.
- Improved energy efficiency: Regular cleaning and maintenance of insulation and cladding can optimize thermal performance, reducing energy consumption for heating and cooling.
- Enhanced safety and structural integrity: Addressing potential hazards like loose fasteners, corrosion, or roof leaks ensures the building’s structural stability and safety for occupants and equipment.
- Reduced repair costs and downtime: Proactive maintenance helps catch small problems before they become costly repairs, minimizing downtime and disruption to your operations.
- Preserved aesthetic appeal and value: Regular cleaning and proper care maintain the PEB’s visual appeal, contributing to its overall value and marketability.
PEB Structure Lifespan and Durability
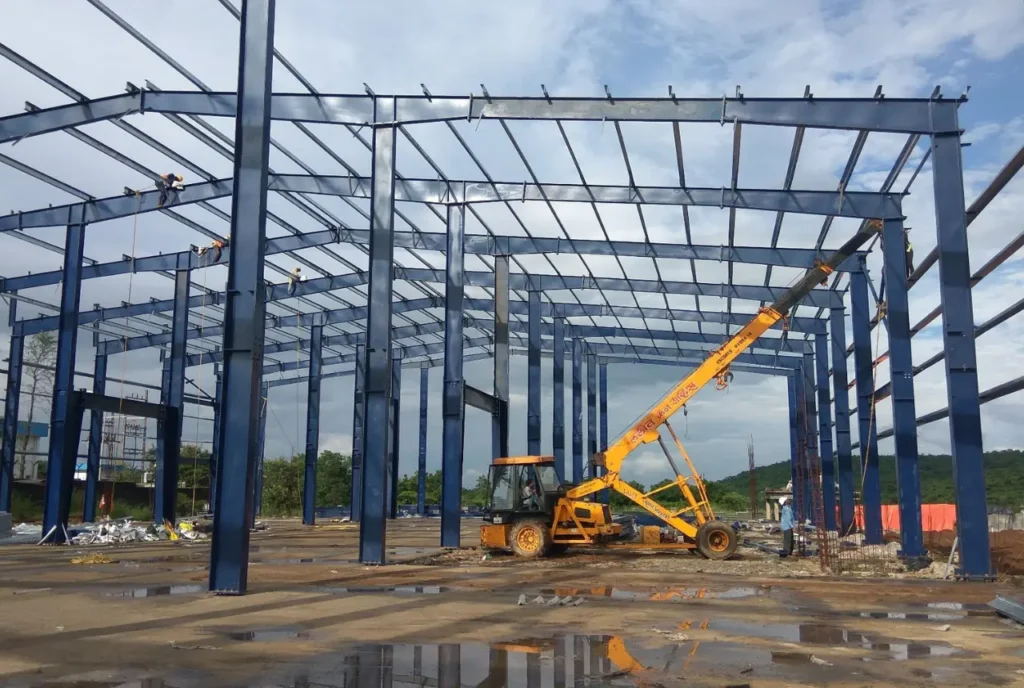
The lifespan of a PEB is influenced by several factors:
- Design: A well-engineered PEB considers factors like wind load, snow accumulation, and seismic activity. Proper engineering practices ensure a robust structure that can withstand these stresses.
- Materials: High-quality steel with proper coatings and corrosion protection contributes significantly to a PEB’s longevity. The choice of cladding materials also plays a role, with insulated panels offering better durability compared to basic metal sheets.
- Construction: Careful construction practices, including proper installation techniques and adherence to design specifications, are crucial for long-term performance.
- Environment: The surrounding environment, including factors like harsh weather conditions, air pollution, and exposure to chemicals, can impact a PEB’s durability.
However, proper maintenance is the key to maximizing a PEB’s lifespan. Regular inspections, cleaning, and addressing potential issues promptly can significantly extend its life and minimize the need for major repairs.
Typical lifespan ranges vary depending on factors like the points mentioned above and the type of PEB:
- Single-skin PEBs: 20-30 years
- Double-skin PEBs: 30-50 years or more
It’s important to note that PEBs can also be built with recycled steel, contributing to their sustainability aspects. Additionally, proper maintenance practices can further enhance their environmental footprint by minimizing resource consumption and waste generation.
PEB Structure Inspection and Testing
Regular inspections by qualified professionals are crucial for ensuring the safety, integrity, and longevity of your PEB. These professionals are trained to identify potential issues and recommend appropriate actions.
There are several types of inspections:
- Visual inspections: These involve a thorough visual examination of the PEB’s components for signs of damage, corrosion, loose fasteners, or leaks.
- Non-destructive testing (NDT): This utilizes specialized techniques like ultrasonic testing or magnetic particle testing to detect hidden flaws in critical components without damaging the structure.
- Structural analysis: Involves advanced methods using specialized equipment to assess the overall structural integrity of the PEB, particularly after significant events like earthquakes or heavy snowfalls.
The frequency of inspections depends on various factors like:
- Usage: High-traffic or mission-critical facilities may require more frequent inspections compared to low-use storage buildings.
- Environment: Buildings exposed to harsh weather or corrosive elements need more frequent checks.
- Age: As the PEB ages, inspections become more crucial to identify potential age-related issues.
During these inspections, specific areas receive extra attention, including:
- Connections: Bolts, welds, and other joining elements are crucial for structural stability and require careful inspection.
- Welds: Checking for cracks, porosity, or other weld defects is essential for ensuring structural integrity.
- Cladding: Inspecting for corrosion, loose panels, or leaks is important to maintain the building envelope’s functionality.
It is vital to document all inspection findings, including observations, photographs, and recommendations. This documentation serves as a valuable record for future reference and facilitates taking corrective actions promptly and efficiently.
PEB Structure Cleaning and Painting
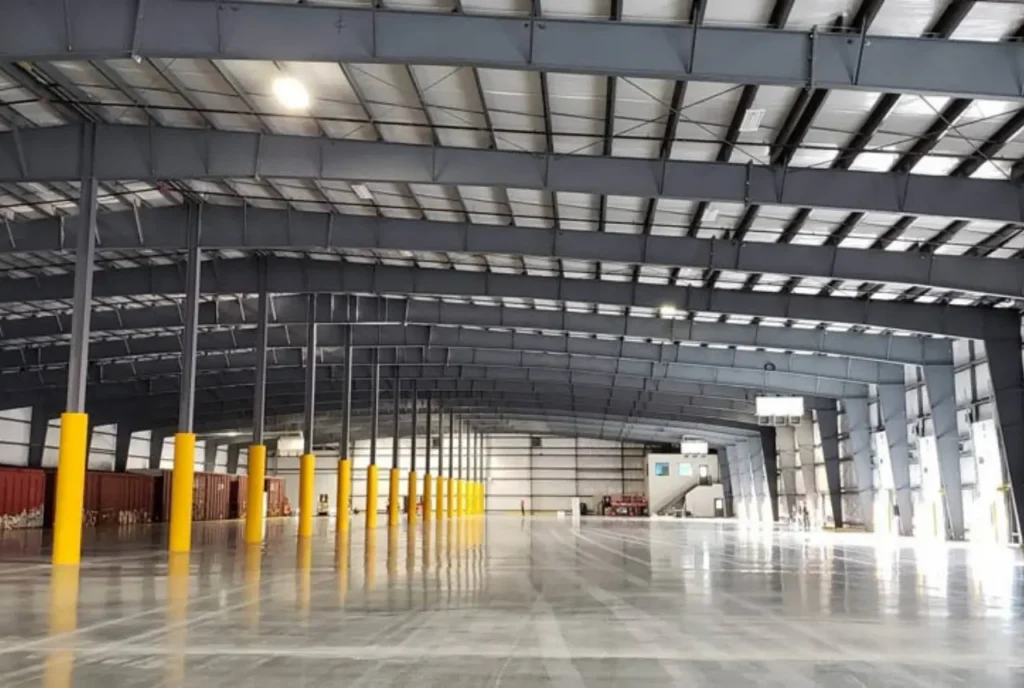
Regular cleaning of a PEB is crucial for maintaining its aesthetics and preventing premature deterioration. Dirt, dust, and other contaminants can trap moisture, leading to corrosion and reducing the lifespan of the cladding.
Cleaning methods depend on the cladding material and the type of contaminants:
- Metal sheets: Low-pressure washing with a mild detergent solution is typically sufficient. Avoid harsh chemicals or abrasive scrubbing techniques that can damage the surface.
- Sandwich panels: Follow the manufacturer’s recommendations for cleaning as their surfaces can be more delicate.
Cleaning frequency depends on the environment and usage:
- High-pollution or coastal areas: Clean more frequently (quarterly or biannually) to prevent salt buildup and corrosion.
- Low-traffic or rural areas: Annual cleaning might suffice.
Painting can enhance the visual appeal of your PEB and provide additional protection against corrosion. However, proper surface preparation is essential:
- Cleaning: Remove dirt, dust, and any existing paint.
- Surface preparation: Address any rust or damaged areas through scraping, sanding, or priming.
Paint selection is crucial. Choose a high-quality, weather-resistant paint designed for metal buildings. Opt for environmentally friendly options whenever possible.
Application methods should follow industry standards and manufacturer recommendations for optimal performance and safety. Be mindful of environmental regulations regarding paint disposal and potential emissions during application.
By prioritizing regular cleaning and painting with proper techniques and materials, you can ensure your PEB maintains its aesthetics, integrity, and lifespan for years to come.
PEB Structure Repair and Renovation
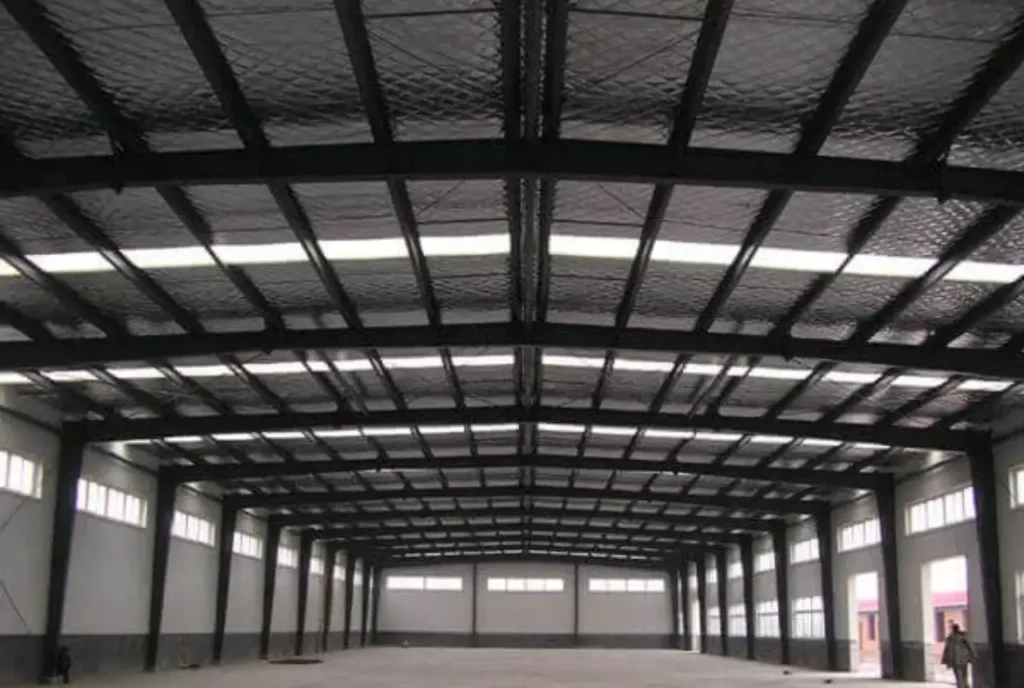
Despite proper maintenance, PEBs can be susceptible to damage over time. Common issues include:
- Corrosion: This can occur on steel components due to exposure to moisture, chemicals, or salt.
- Leaks: These can develop in the roof, walls, or cladding due to damaged sealant, loose fasteners, or punctures.
- Structural issues: These can arise from factors like overloading, design flaws, or environmental events like earthquakes.
It’s crucial to identify signs of damage promptly and take immediate action. This could involve:
- Visually inspecting for signs of rust, cracks, leaks, or loose components.
- Consult a qualified professional to assess the extent of damage and recommend appropriate repairs.
Professional repairs are essential for ensuring the structural integrity and safety of the PEB. Attempting DIY repairs, especially for structural issues, can be dangerous and exacerbate the problem.
Beyond repairs, PEBs offer various renovation options:
- Upgrading insulation can improve energy efficiency and reduce heating or cooling costs.
- Adding skylights can introduce natural light and enhance aesthetics.
- Modifying interior partitions can adapt the space to changing needs.
However, cost considerations are crucial. Repairs can range from minor touch-ups to extensive structural work, while renovation costs depend on the complexity and scope of the project. Prioritize thorough assessments and obtain quotes from qualified professionals before undertaking repairs or renovations.
PEB Structure Design and Fabrication
Choosing a reputable PEB manufacturer is crucial for long-term satisfaction. Look for companies that prioritize:
- High-quality materials: Certified steel with proper coatings and adherence to relevant standards.
- Advanced fabrication techniques: Utilizing modern equipment and skilled personnel for precise and efficient manufacturing.
- Strict adherence to industry standards: Ensuring structural integrity, safety, and compliance with local building regulations.
By selecting a manufacturer committed to these aspects, you can be confident that your PEB is built with long-term durability in mind. This translates to lower maintenance costs, fewer repairs, and a structure that stands the test of time.
Conclusion – What did we learn?
In conclusion, PEBs offer a versatile and durable building solution. However, proper maintenance is crucial to maximizing their lifespan, performance, and safety. By following the guidelines outlined here and consulting with qualified professionals, you can ensure your PEB remains a valuable asset for years to come.